If you have any experience in business management, then the chances are that you're aware of both Material Requirements Planning and Enterprise Resource Planning. Although they have similarities, they are also different. This article will highlight what each system is and help you decide which one is the best for you.
MRP systems
Both MRP and ERP are software items designed to assist you in the running of your business by helping you to forecast better and bring cohesion between your chosen business priorities. MRP has a strict manufacturing focus with the intention to meet the following three objectives:
- To make sure raw materials are available for manufacture and outputs are available for customer delivery
- Ensure the least possible material and product in store
- To design manufacturing tasks, buying tasks, and delivery itineraries.
The benefits of MRP are that it allows total control and efficient administration of stock, overall equipment effectiveness, buying, and manufacturing. The focus for MRP is the manufacturing process, where it's designed, with people working in these departments in mind. An MRP system would use a forecast to order the required materials to arrive on an appropriate date for manufacturing to continue seamlessly. MRPs are also capable of integrating with supplier's systems to ensure more efficient supply chain management.
The drawback of MRP systems is that they rely on highly accurate data input. Any discrepancies in the data entered can result in problems like delays or under and over-deliveries. Of course, the knock-on effect of issues like these is the loss of business or cash flow problems which can be highly detrimental to any business. So while MRPs can be highly effective in letting manufacturers know what is needed and when and can be instrumental in a well-run operation, there are possible pitfalls that need to be considered.
ERP software 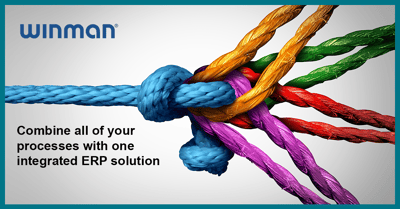
Enterprise Resource Planning systems differ from MRPs in that they integrate every part of the business rather than just from the manufacturing process. The elements of retail and distribution can be linked to the system, giving you and the customer a cleaner, more transparent process from start to finish.
ERP can track manufacturing processes in the same way as MRP, the main difference is, it also has the functionality to manage areas such as accounts, sales, customer services and more. Management will be able to gain a full clear picture of how their business is operating from one system and can use the data to make more informed, better-quality decisions about the future of their enterprise. Real-time costs, status, and customer updates allow business managers to react quickly also decisively with accurate information.
For example, by bringing in sales forecasting into the process, a business can prepare its materials and work hours to respond to that order. Another potential benefit would be the ability to provide the ever-popular end-to-end tracking, from order to delivery estimate. In terms of process manufacturing, the use of an ERP allows for increased efficiency, leaner manufacturing, and a more agile and flexible business.
Conclusion
When compared to an MRP system alone, a well-constructed and maintained ERP would beat it hands down. While of course, a quality MRP will make a business owner's life easier, an ERP not only allows even more efficiency but helps highlight insight into other areas of business, potentially not only making life easier but the business more profitable and future-proof.